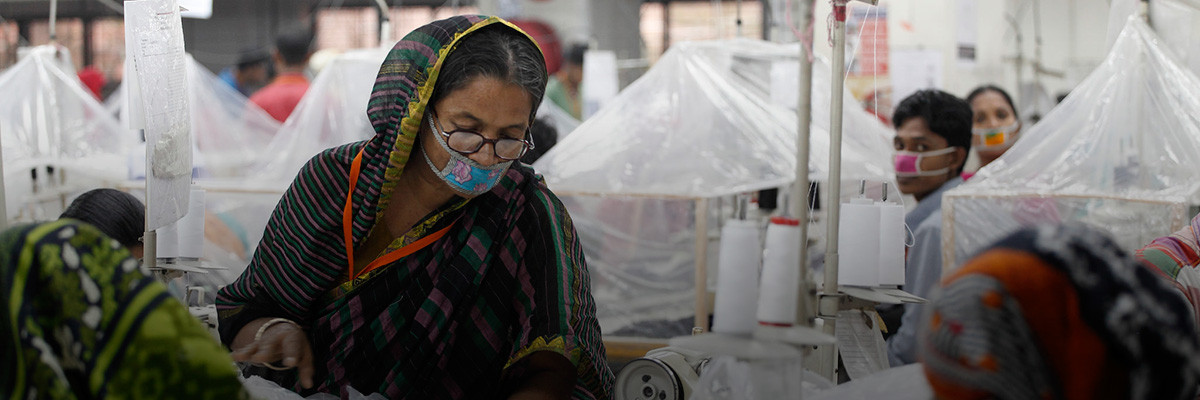
This photo is courtesy of the Better Work Programme.
Authors
-
Cassi Wright
Former Associate, BSR
During my most recent trip to Bangladesh to assess the impacts of the ready-made garment sector, I discovered signs indicating that socially responsible factories are beginning to strategically link employee engagement to human rights and increased production. And now is an opportune moment for international companies, government, and civil society to collaborate on human rights and sustainable development in the country: In 2014, the government of Bangladesh and the Bangladesh Garment Manufacturers and Exporters Association announced targets to double revenues from the ready-made garment export sector from US$24 billion in 2012 to US$50 billion by 2021.
This growth target offers significant economic opportunities for the country, communities, and businesses, but also means, among other issues, that factories must ensure robust employee engagement strategies to retain workers and enhance productivity.
My research in Bangladesh demonstrated that traditional Western supply chain management approaches designed in corporate offices are not always effective. For long-term impact and to avoid unintended negative consequences, companies must tap into local knowledge to create productive and appropriate employee engagement methods customized to the cultural and geographic context. This requires thinking outside the “Western box.”
I observed local best-practice employee engagement approaches within several socially conscious Bangladeshi factories.
Living Wages
In 2008, a factory influenced by Western companies to pay a living wage increased salaries by 15 percent to help close the gap between the legal monthly minimum wage, 5,300 taka (US$68), and the cost of living in Bangladesh. The result was that workers at other factories began demanding the same, creating social unrest. This angered neighboring factories, and placed pressure on both the factory and the industry association regarding the above-market wages. Additionally, local landlords surrounding the factory increased workers' rent prices proportionally to the wage increase, which neutralized any additional earnings. To alleviate the conflict and support a lower cost of living for workers, the factory’s local solution was to reverse wages back and open up a fair trade shop on the factory campus, which offered 300 basic items at wholesale prices. This lowered the cost of living of workers and increased their discretionary income without an actual wage increase.
Female Health and Hygiene
Change Associates, BSR’s HERproject partner in Bangladesh, found that the majority of women garment workers suffer from reproductive tract infections from using leftover cloth strips in place of expensive sanitary napkins. The scrap cloth can contain fungus, parasites, dust, and dye chemicals. Factory management discovered this problem because women were flushing the material down the toilet, causing regular clogs. Local HERproject peer-based training provided the women workers with education on how to use and dispose of sanitary napkins, and after an 18-month negotiation, the factory agreed to provide sanitary napkins at a 50 percent discount. Just 3 months later, managers reported clear sewage lines and new requests to empty bathroom garbage bins—the fastest behavior change ever experienced by the factory. The health benefits of improving feminine hygiene and leveraging the factory as a new distribution channel for products resulted in increased business performance through reduced sick time and absenteeism, increased productivity, and decreased maintenance time and costs.
Community-Based Daycare Centers and Preschools
Bangladeshi law requires factories to provide a daycare center for workers with children under age 6, but mothers often do not use the centers due to a lack of trust in the quality of services, building safety concerns, and cultural preferences for home care. This means that, sometimes, when a suitable relative or neighbor can’t be found, children are left home alone. Although rare due to resource constraints, workers do express confidence in community-based daycares and preschools, which provide a sense of security that children are receiving high-quality care and early education in a safe, nurturing environment. Public-private partnerships for community-based childcare can close this resource gap, offering increased capacity, attendance hours that correspond to shift schedules, nutritious meals, trained caregivers, and subsidized costs. Preschools in Dhaka, such as ones co-sponsored between international companies and BRAC, demonstrate a successful, balanced partnership combining the powers of corporate funding and NGO expertise in a local context.
Corporate Social Mission
Another factory has a social mission and local customs built into its DNA. The factory was founded by a local Muslim civil engineer to create economic opportunities for impoverished people in his community. Community members who live in the district are given priority for job opportunities, welfare officers talk to workers on the production floor twice a day to discuss concerns, and the managing director personally reviews submissions from an anonymous suggestion box. The factories provide onsite, subsidized medical facilities for workers and children, as well as flexible maternity leave. Nodding to local custom, the company distributes special food packages and festival bonuses during holidays and prayer time for practicing Muslims twice a day, in addition to regular breaks (non-Muslims may use the time to rest). During prayer time, the power is turned off, stopping production. Management found that prayer time and the pre-prayer ritual of washing hands and face serve as a mental and physical refresher that increases productivity, which typically decreases after 3 hours of working without breaks. The factory’s statistics exceed industry averages, with less than 1 percent turnover, a 95 percent return rate from maternity leave, and a large number of workers who have stayed with the company for 10-15 years.
Global supply chains link the developed and developing world, but drastically different circumstances and local contexts mean that typical Western solutions to business challenges often are not applicable. The corporate office or boardroom cannot identify every challenge—it is essential that problem solving is developed at the local level. By fostering flexibility of approaches and decentralization to the factory level, companies and their suppliers can create long-term positive impacts for workers, driving business benefits and contributing to an inclusive economy.
Let’s talk about how BSR can help you to transform your business and achieve your sustainability goals.